Key Projects
Aero Automation
An intuitively designed graphical interface, seamlessly integrating robust macros and knowledgeable components to expedite aerodynamic design processes. The multifunctional macros adeptly handle tasks such as managing part and geometry attributes, creating and managing solids, modifying geometry, overseeing publications, handling data read/write operations, facilitating image exchange, managing FEA sensors, and interfacing with CFD and WT systems.
Within this user-friendly GUI, effortless access is granted to a curated collection of catalog items, strategically devised to enhance both capability and speed. At your fingertips, it unveils a suite of tools empowering aerodynamicists and designers to navigate the intricacies of developing a competitive car by focusing on the shape rather than the toolset and that aligns with FIA regulations.
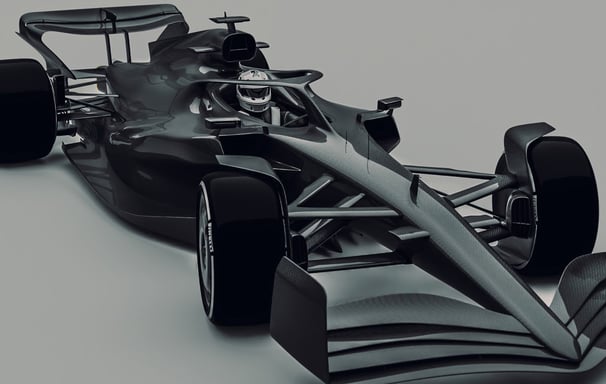
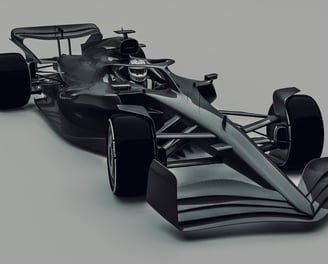
Masterclasses
Facilitated engaging masterclasses and workshops, delving into the nuances of advanced aerodynamic surfacing. These sessions provided comprehensive insights into surfacing methodologies and practical guidance on leveraging developed tools to elevate shape quality and streamline processes. Noteworthy instances include conducting these sessions within the dynamic environments of both Aston Martin and Airbus aero departments.
A special highlight was the exploration of CATIA's impressive suite of digital morphing tools. These tools, adept at utilizing points, curves, and surfaces, emerged as invaluable assets for swift shape modifications while preserving the intrinsic character and topological features of the input shape.
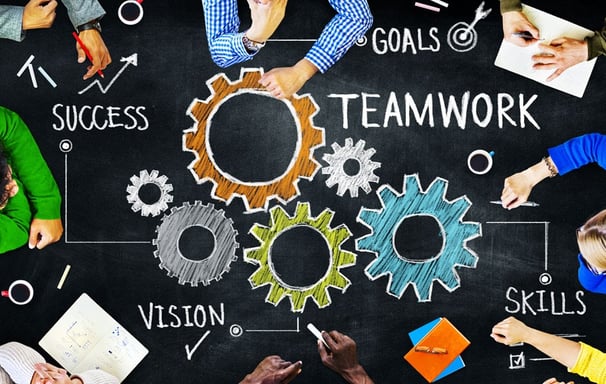
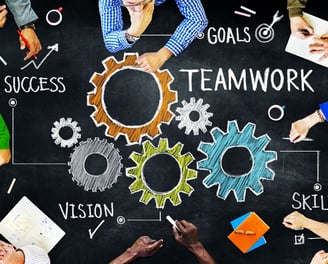
AIRGEOM
AIRGEOM stands out as a specialized toolset crafted for the intricate task of advanced morphing of an aircraft wing, encompassing spars, ribs, and stringers. Its functionality extends to the subsequent redefinition of critical assembly data, crucial for the final assembly phase. The primary objective behind this effort was to reshape the jig configuration, aiming to enhance aerodynamic efficiency significantly.
This collaborative initiative unfolded within a multi-disciplinary team, fostering synergy across various domains, including manufacturing and assembly.
The result of the slight changes in flight geometry shape can result in significant fuel cost savings across the fleet of aircraft.
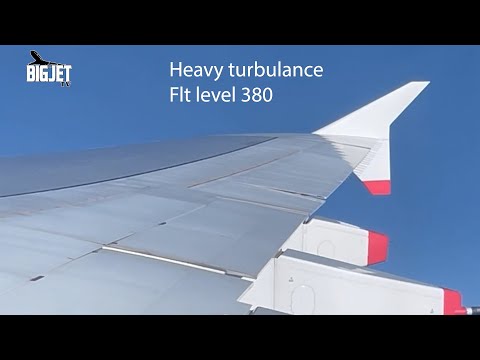
Wing Integrated Smoothing Environment
WISE emerged as a collection of CATIA Knowledgeware geometry components complemented by Visual Basic code. Its purpose was to handle the import of point sets featuring sectional profiles and establish a swept transonic wing configuration. This allowed for dynamic modifications to the sections, including adjustments in height, twist, scale, and camber, thereby enhancing the chordwise and spanwise smoothness of the surfaces.
The toolset facilitated on-the-fly execution of 2D CFD codes, with the ability to overlay pressure distributions on the geometry. These surfaces, requiring minimal rework, became valuable for subsequent CFD or wind tunnel assessments. Moreover, they served as a foundational reference for the smoothing process in aircraft manufacturing.
The primary objective of this toolset was to expedite wing surfacing tasks for both seasoned professionals and newcomers, all the while elevating the overall surface quality.t.
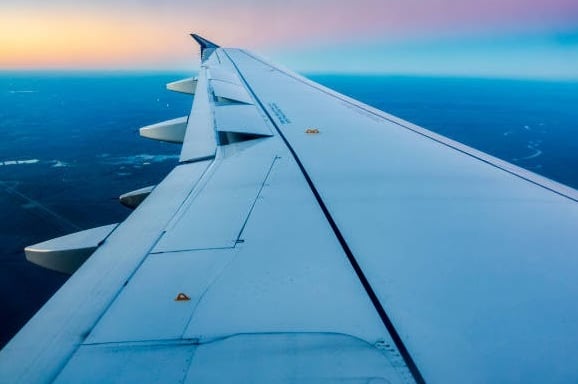
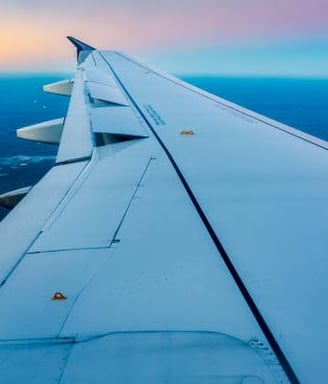
Parametric Design & Class A Surfacing
During my time in the aircraft industry, I focused on designing wings for civil and military transport aircraft at Airbus in Filton, Bristol (formerly British Aerospace). This involved tasks like writing custom code for geometry modifications, shaping designs through CAD, assessing changes using CFD methods, and guiding selected designs through wind tunnel testing.
A significant part of my work aimed at improving existing aircraft, where attention to detail in surface quality for wind tunnel testing and aircraft manufacture was crucial. This involved maintaining Class A quality, paying careful attention to surface smoothness, patch count, and isoparm layout to meet the highest standards.
My time within Formula One Racing aerodynamics spent on improving skills, capability and efficiency where the parametric and knowledgeware methods were exploited to deliver high quality shapes for CFD, wind tunnel or the track.
Motivated by a genuine passion for achieving excellence in aerodynamic shapes and simplifying processes through CAD automation, I explored automation and knowledgeware. This exploration led to the development of tools tailored to the specific needs of aerodynamic users.
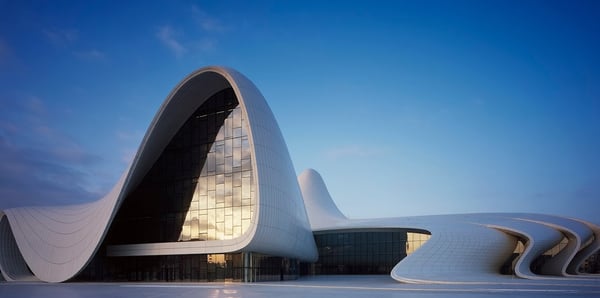
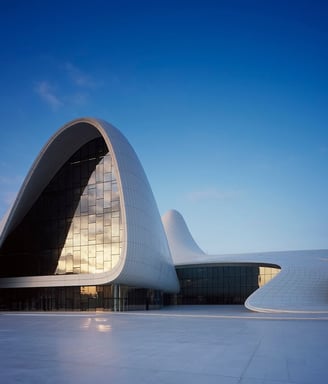
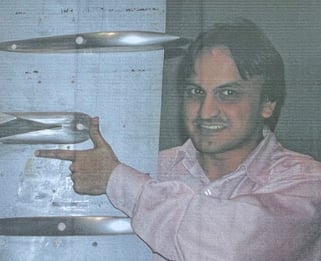
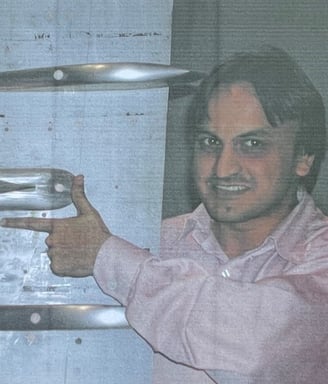
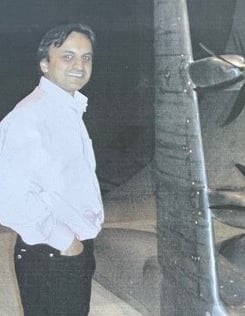
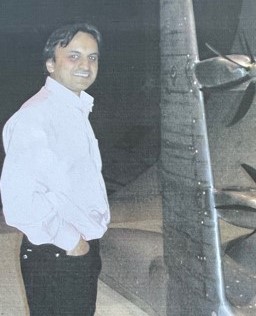
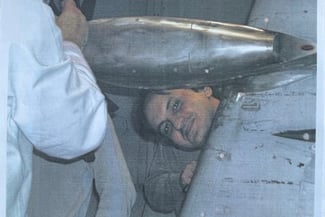
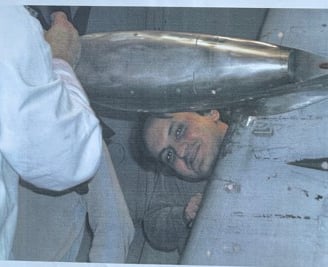